You have just unpacked your latest purchase... a beautiful Carbatec 15" thicknesser. You've cast aside the unread manual and have dived head-first into the assembly. All bolts tightened, blades aligned, and you head straight for the pile of waiting timber. What a magnificent collection of exotic hardwood, just pleading to be converted into a three-meter-long dining room table. You plug in your new weapon and throw your first victim to the spinning blades.
It's hard to recall what first hits you, the ear-piercing scream of the blade hitting solid timber, then the mulching of the waste material, or the fact that the workshop rapidly fills with re-mulched hardwood shavings. As you cough up some dust, you think to yourself, "Pity the quality of the milled finish isn't exactly what I expected."
The Importance of Dust Extraction
Professional woodworkers have known for decades that an adequate dust collector is one of the most important pieces of machinery in the workshop. It's only us, serious DIYers, that seem to question their wisdom. A clean, dust-free workplace is not only safer but far less work in the long run. There is less cleanup and less airborne dust, which is very important in the finishing stage.
Another important fact is that it is far better for your machinery to have these dust and shavings removed. Other than being forced back around the cutting area and affecting the quality of the work, fine dust particles can be sucked into electrical components, build up on moving parts or pile up in areas underneath your machinery, becoming a fire hazard in the process.
Worst of all, these particles can find their way into your lungs. Dust collection is NOT a replacement for PPE (Personal Protective Equipment,) but it reduces the dust in your immediate work area, which means your PPE is going to work much more efficiently too.
The sad fact is that running machinery without dust extraction may affect your warranty if something does go wrong. "Why didn't I read the manual?"
Dust Collector versus Vacuum Cleaner
Most workshops have access to a vacuum cleaner, either a dedicated unit or the household unit (only if you don't get caught)! They're great for cleaning the car and even getting the dust off the workshop floor. Isn't it annoying when a little offcut or long splinter gets stuck in the hose? You hear the motor start to struggle and whine, and you proceed to wave the end of the hose around in some strange ritual that will hopefully dislodge the offending piece. So what makes us think that by hooking this same vacuum to a heavy-waste-producing machine, the results are going to be any different? It really comes down to a simple rule: vacuum cleaners are made to vacuum, and dust collectors are made to extract and collect.
Vacuum cleaners work on the principle of a low volume of air travelling at high velocity, while dust collectors work on a high volume of air travelling at low velocity. Vacuums are great for lifting small quantities of fine dust from the bottom of your carpet through a small-diameter hose.
Dust collectors, on the other hand, are designed to cope with a large quantity of waste constantly being produced, and the large diameter hose means no blockages, provided you have enough air volume.
Air volume is measured in Cubic Feet per Minute (CFM), and even a small, basic 1HP dust collector will give you 600+ CFM of airflow. Most cutting/drilling machinery will require at least 600CFM of extraction. Edge planers or jointers need slightly more (depending on size), but large milling machines such as thicknessers will require at least 800-900CFM at the extraction point on the machine. This is an important consideration before taking the plunge.
Flexible Hose
Most woodworking machinery will be provided with a large-diameter extraction connection. This will usually be a 4" or 5" (100mm or 125mm) connection. This should marry nicely to your dust collector, directly or with some adaptor.
An important factor in the operational efficiency of your dust collection system is the positioning of the dust collector in relation to the machine. Many people have designed elaborate systems, utilising Y-pieces to increase the number of machines connected, blast gates (that switch to close off the airflow to one or more points), and running many meters of flexible hose up the wall and across the ceiling, back to the dust collector. When they switch the system on, they wonder why the suction at the far end is barely audible, unlikely to have the capability to suck several kilos of timber waste.
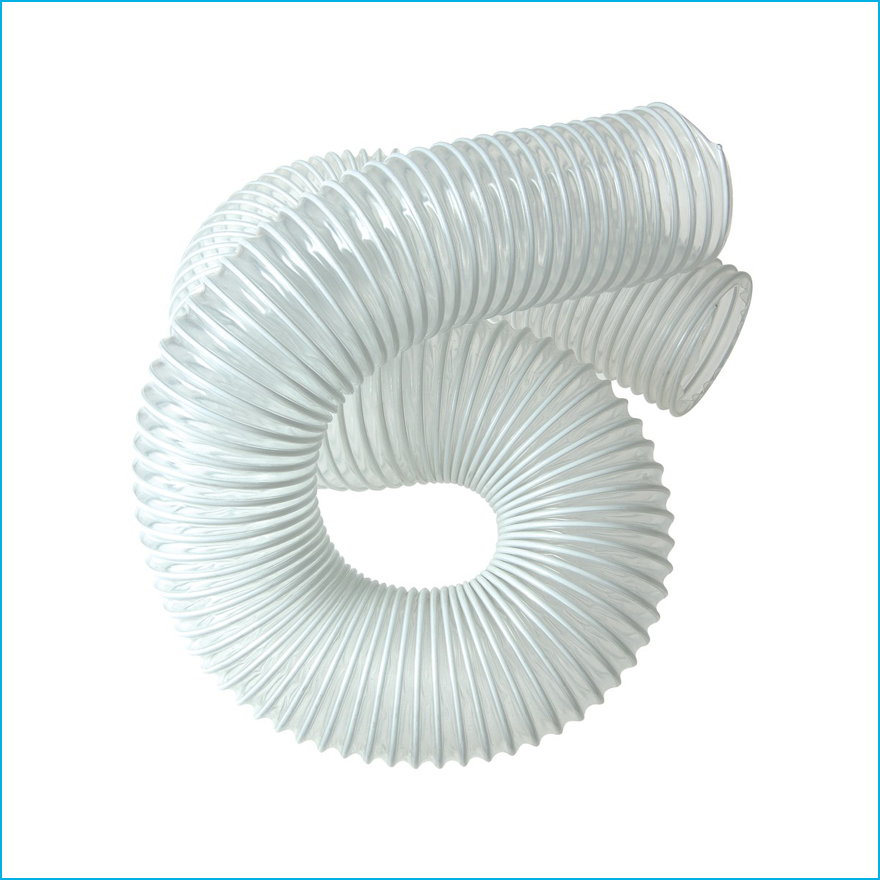
For every metre of flexible hose you run, you will lose approximately 10-20% of your volume (CFM). For every bend and fitting, you will lose even more CFM. Do the math - just three metres of flexible hose, and a third of your suction is gone... but where? Have a look at the diagram below.
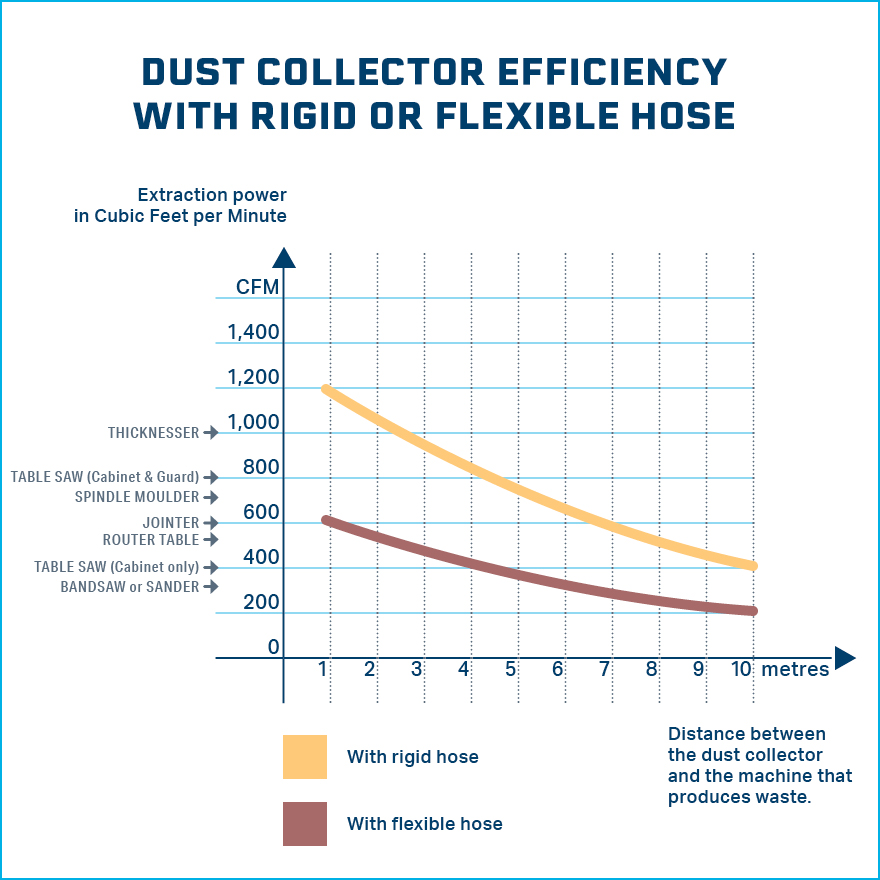
Have a close look at the flexible hose. Every single ridge of the hose that the air has to run across is disrupting the efficient flow of the air and, in turn, the waste. If you want to run a larger system, make sure you have enough suction volume at the start to ensure you don't run out at the business end. Professionally designed and installed workshop systems use rigid metal pipes, with a smooth finish and engineered bends to increase efficiency, and they run very high-capacity dust collectors, allowing all machines to be run simultaneously. Suction loss on these systems is usually only about 1-2% per metre, but the purchase and setup cost is high. The straighter and shorter you can keep your dust collection system, the better. Remember that bigger CFM is always better.
Dust Collector Safety
One hazard that is often overlooked in dust extraction equipment is the buildup of static electricity. The dry timber particles rubbing the inside of the flexible hose are constantly building a static charge, in the same way rubbing a plastic comb through your hair will build up a static charge. Static, when it discharges as a spark, is just one of three parts required to create an explosion. The other two parts are fuel (in the form of fine dust particles) and air.
Explosions in dust extraction systems are rare, but they do happen. More often, it's the painful 'crack' of the static on our fingertips that reminds us of this potential danger. A simple solution is to ground your system. Fitting a grounding kit to the inside of the flexible hose and connecting the wire to both the machine and the dust collector will minimise or eliminate static from the system.

GK-50
Selecting Your Dust Collector
Determining which dust collector is right for you will depend heavily on what you want to do with it. If you only want to hook it up to your table saw, a very basic unit will do the job. However, if you want to connect it to your thicknesser or jointer, you need to start at a 2hp unit with a higher CFM rating and a larger waste-holding capacity.
It's important to think ahead about what your future requirements will be. If you plan to add more machinery later and don't want to move your dust collector between machinery, invest in a larger unit that will allow you to add extra points without sacrificing too much performance. Be honest with yourself and it won't end up costing you more in the long run.
CFM Requirements per machine (Basic Guidelines)
- Bandsaw: 300 CFM
- Table saw: 400 CFM (cabinet connection only)
- Router table: 500 CFM
- Jointer or small thicknesser: 600 CFM
- Spindle moulder: 700 CFM
- Table saw: 800 CFM (cabinet and overhead guard)
- Lathe: 800 CFM
- Large Thicknesser: 1000 CFM
These requirements are approximate and are, of course, heavily dependent on your usage and the type of material being used.
But what about an existing system you want to refine? Go back to basics, strip out some of the fittings, straighten the lines and simplify the whole design. A couple of percents here and there will help.
Note also that these specs refer to the extraction requirements at the machine (where the hose meets the machine's dust port), not the listed capacity of the dust collector. To work this out, you need to take into account the distance between the collector and the machine, the machine type and the type of ducting used (flexible or rigid), as well as fittings, bends, etc. This way, you can calculate an approximate line loss value across the entire system. Now is a good time for you to get out your crayons and paper...
Planning and Designing your Dust Collection System
You need to do a good scale drawing of your workshop layout, position your machines in their ‘in-use’ location, figure out how you want to connect them and decide where your dust collector will reside. Try to keep the heavy producers of waste (like thicknessers, lathes etc.) closer to the dust collector. Draw out your desired plan, keeping the main line as straight as possible. List your ‘Y’ Junctions, ‘T’ pieces, connections, bends and blast gates, and total your hose requirements.
To calculate your approximate line loss across your system, use the following rules of thumb:
- Every meter of 4” (100mm) flexible hose will reduce your CFM by 7-10% per metre. Keep it short.
- 90° bends will restrict airflow by 3-4% each.
- ‘Y’ Junctions will divide the airflow in half if both sides are left open (use blast gates to switch off the unused side). A gated “Y” Junction will reduce airflow by 1-2% each.
- “T” pieces are fairly inefficient compared to “Y” junctions. They will reduce the airflow by 3-4% each.
- Stepping down to a smaller diameter, will increase the velocity but will lower the CFM airflow considerably. A good example would be trying to suck a lung full of air through a straw. It works, but it's hard work, and you wouldn’t want to do it all day. Your future or current dust collector agrees. Use minimal reducers, and try to keep them near the end of the line, near the machines that produce smaller amounts of dust (scroll saws, mitre saws etc).
- KEEP IT SIMPLE
Armed with these guidelines, crayon in hand… develop a plan to reduce your dust.
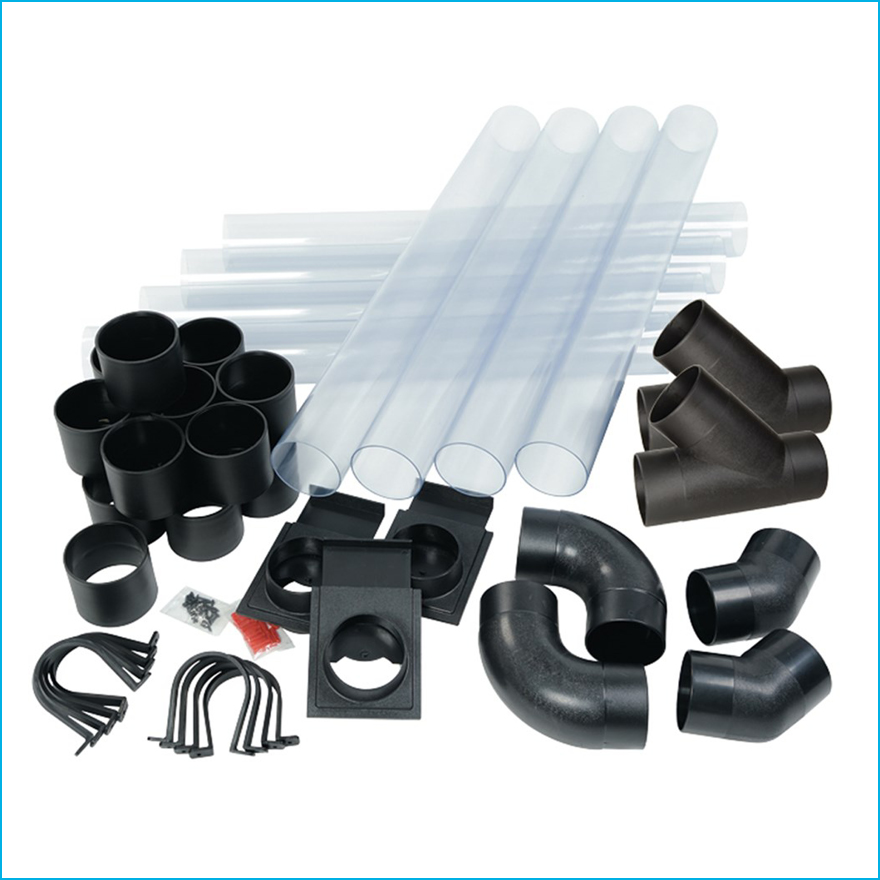
YW-2000B
Metal Ducted Networks
Largely because flexible PVC is such a cheap and simple option, metal ducting has been out of the reach of most small workshops or backyard sawdust manufacturers. Carbatec have developed a great value offering designed for just this market. We have been working closely with Eximo-Speedlock to put together a versatile DIY metal ducting network that will marry easily to existing flexible networks, or make a great starting point for a new setup. We have chosen Speedlock for their respected reputation in the industrial market and their understanding of the DIY market's special requirements.
The efficiencies you gain with rigid ducting versus flexible PVC are dramatic. Using our rules of thumb listed above, with rigid ducting we'd now have:
- Line loss will be only about 1% per metre.
- 90° bends will restrict airflow by only about 1% each due to their larger radius and constant diameter.
- ‘Y’ Junctions will still divide the airflow in half if both sides are left open (use blast gates to switch off the unused side). A gated “Y” Junction will reduce airflow by around 1%.
- “T” pieces are not used with rigid ducting due to their inefficient properties.
- Stepping down is usually done through a long conical reducer, which is far more efficient. We recommend placing these near the end of the system.
This sort of rigid ducting network would have enough straights, bends, corners, junctions and fittings to put together a pretty substantial and professional dust system in a workshop up to about six metres long, with three outlets. Overall, you'd be looking at losing only about 15-17% total CFM. The equivalent system in flexible PVC would reduce your CFM by about 70%.
Eximo-Speedlock systems are very DIY-friendly and adaptable. Extra components can be added or removed at any time and are more affordable than you may think.
Types of Dust Extractors
Technically speaking, the commonly used dust collectors in woodworking workshops are broken down into two main categories: bafflechamber and cyclonic separation. There are many variations on a theme, but usually, these two are what you will find.
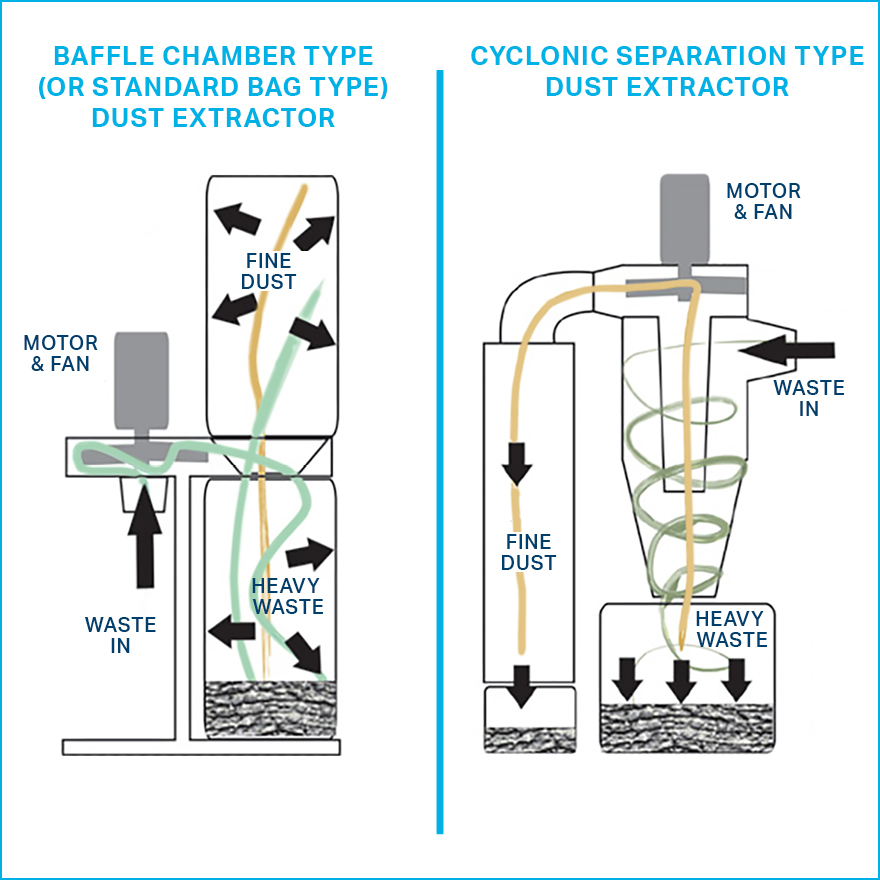
The Baffle Chamber Type
The more common and less expensive Baffle Chamber (or standard bag type) dust collector uses a motor to spin a centrifugal impeller that- through its clever blade design - sucks air in through the centre of the fan and pushes it out toward the sides of the fan. Manufacturers design dust collectors so that the inbound waste follows this air path through the impeller and into a collection chamber. The change in air direction once waste gets to this chamber causes the heavier waste to fall down and the lighter dust particles to rise up. These are caught in a filter on the top. This filter can be either a cloth or felt bag or a more elaborate pleated filter cartridge.
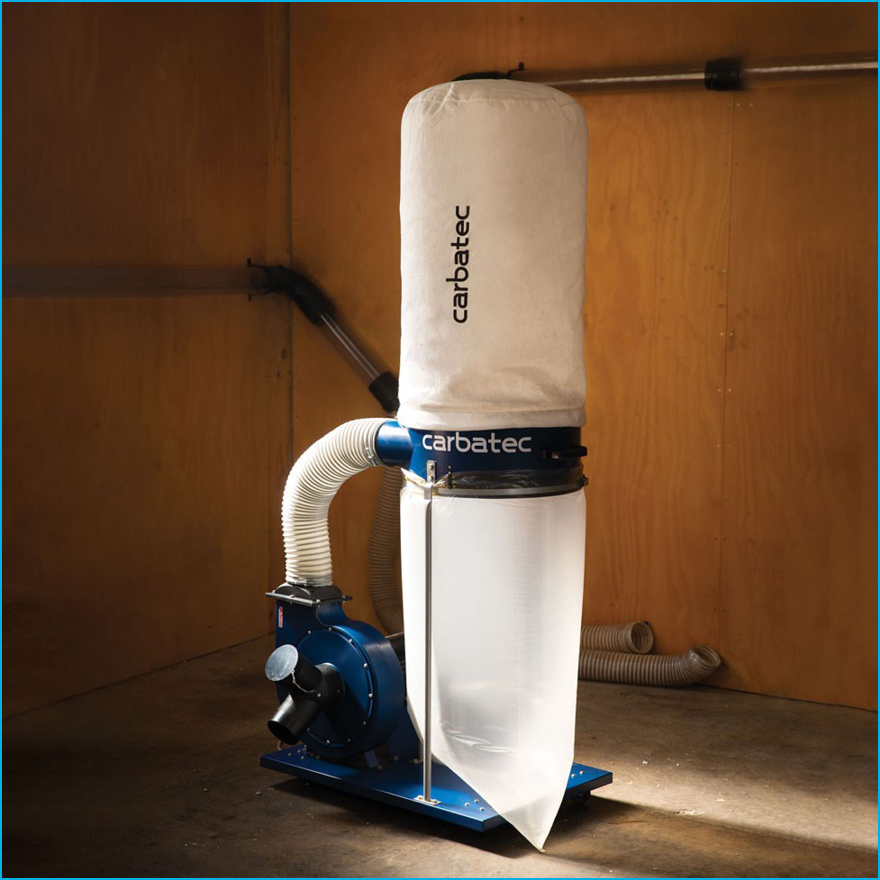 DC-1200P
The Cyclone Type
Cyclonic Separation is not a new concept. It has been available for industrial use for many years but has only become accessible and affordable to the general public within the past decade. Cyclones differ from standard bag extractors in many ways. Their design and build are far superior, and the technology involved is far more efficient. Again, a motor is used to spin a centrifugal impeller, but whereas the impeller on the standard bag extractor was in line with the waste flow, the cyclone has two different paths. The airflow path pulls the waste into the collection chamber, but from there, it uses directional baffles to divert waste material. Basic theories of thermodynamics and some high-end aspects of quantum physics come into play, and effectively the waste flow path sees the material spin rapidly around the outside cone, and it's then forced down to the bottom of the collection chamber, leaving the airflow path free of heavy waste. The remaining fine dust particles are then sucked through the impeller and pushed out into a small collection bag. To explain this a little better, we have provided this simple cyclonic separation formula and a diagram.
Cyclonic machines run consistently with maximum efficiency and constant air flow......while traditional baffle chamber-type extractors run less efficiently, with airflow being affected by the various factors we've already looked at.
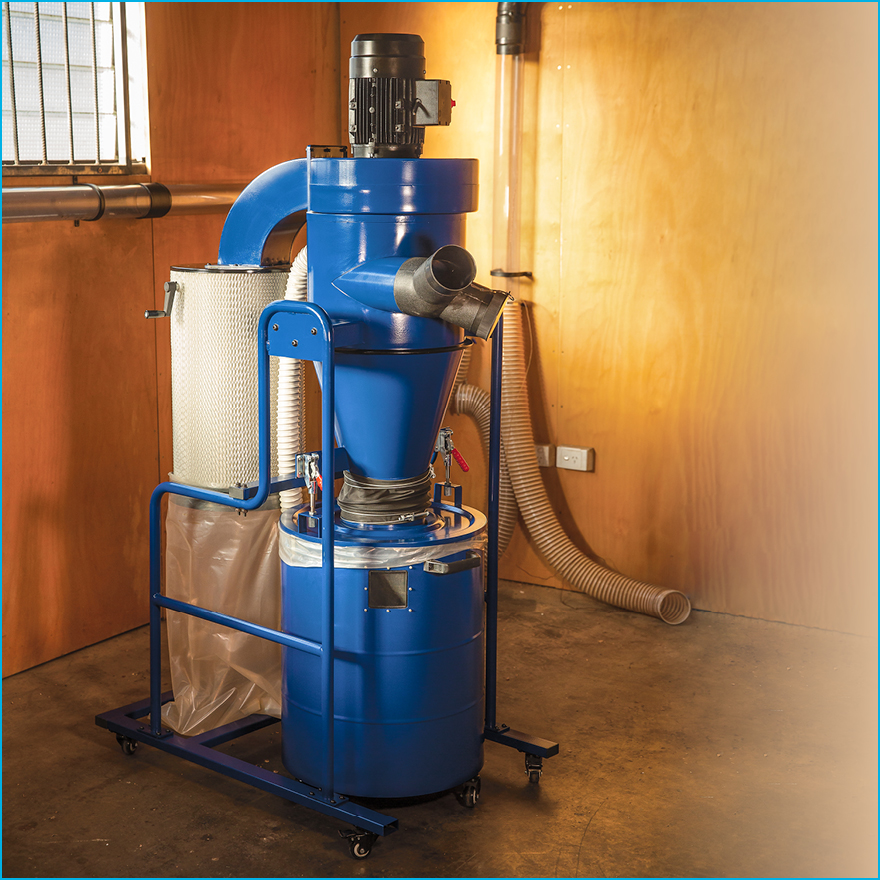 CDC-650P
The main difference between a standard bag system and a cyclone system is performance. Cyclone collectors run at lower CFM rating than equivalent bag-type collectors. This is due to the extreme efficiencies gained in the design. No longer is the actual CFM reading jumpingup and down due to the heavy waste material bouncing off and running through the impeller. The suction pressure being applied to thesystem is constant and uninterrupted. Cyclones efficiently deal with heavy waste material and separate this from the fine dust.
Performance Enhancements For Existing Systems
Cartridge filters.
On a standard bag system, the fine dust is pushed up and forced into the fabric filter bag. This fine dust needs to be cleaned occasionally by hitting the outside of the bag or by blasting it with compressed air. Maybe replacing the tired old filter bag would breathe some life back into your dust collector? After-market cartridge filters can be added to most standard bag-type collectors. A cartridge filter (which looks like a very large car air filter) replaces the standard fitted top filter bag and improves the outward airflow. Its greater surface gives the fine particles a larger area to settle into, and most cartridge filters will have internal cleaning brushes to aid with periodic maintenance.
In-line dust separators are available to reduce the volume of waste material before it gets to the impeller of your dust extractor. These usually sit on top of a large plastic rubbish bin, in line before your collector. These work quite well but will affect the CFM airflow, as mentioned earlier.
Upgrading your existing flexible PVC network to a rigid system will be a huge enhancement. The cost of this upgrade may well be less than buying a larger extractor and plugging it onto your inefficient flexible PVC network (for little or no increase in performance).
So what is my best option?
There is no right answer, but there is always a wrong answer. The best option for both collection networks and dust collections is always going to be dependent on your own collection of machinery, how big your workshop is and where you see yourself in the future. The wrong option is deliberately designing a system that’s ‘just enough’ or not quite enough to do the job. The money you save now will soon be forgotten when comes the time to fix the problems.
Carbatec stores stock a large range of standard dust collectors, cyclone dust collectors, flexible PVC, rigid ducting, PVC and metal fittings for all your dust extraction requirements. Maybe the best option would be to talk to one of our professional staff and ask for some advice. If you have a large workshop or you’re a club with a complicated setup, and you’re looking for a large ducted system, we can organise a professional designer to call and discuss options. They can calculate your requirements, design and install entire systems.
Click on the link below for information and pricing:
See our Dust Control Solutions.
|